Costco is known and loved for its $5 rotisserie chickens. In order to better provide this popular item, Costco has recently moved beyond simply supplying chickens to actually raising them. To do this, it established an enormous chicken operation— including a hatchery, a feed mill, a processing facility, and a network of local farmers who raise the poultry—in and around Fremont, Nebraska. It will eventually produce 2 million chickens a week.
With such a large facility coming into the area, some locals were concerned about issues including the amount of chicken litter, or manure, that the poultry would create and its potential effects on groundwater. In this interview, Jessica Kolterman of Lincoln Premium Poultry, the company formed by Costco to manage its facility, explains how it worked with the State of Nebraska to establish stringent guidelines to make sure that the chicken litter was disposed of in an environmentally safe manner.
Irrigation Leader: Please tell us about your background and how you came to be in your current position.
Jessica Kolterman: I came to the Lincoln Premium Poultry team by way of working for the State of Nebraska. I was working for the Nebraska Department of Agriculture on a temporary assignment with the goal of recruiting this project to the state. After we had achieved that goal, the company hired me to work on implementing the project.
Irrigation Leader: Please tell us about Lincoln Premium Poultry.
Jessica Kolterman: Lincoln Premium Poultry is a company that was formed by Costco to manage the poultry operations of its new facility. Our team was built to accommodate Costco’s goals and objectives, which were to create a food processing facility for chicken, a feed mill, and a hatchery, and then to develop a network of farmers here in Nebraska to raise the poultry. We are working with 80–100 farms. We refer to the combination of the hatchery, the feed mill, the processing facility, and all the farms that are associated with those facilities as a complex.
Irrigation Leader: How large are the new facilities?
Jessica Kolterman: The food processing facility is about 400,000 square feet and the hatchery is about 90,000 square feet. The feed mill produces enough feed to haul out to all our farms in the region.
Irrigation Leader: Were there any concerns about the effects that this increase in poultry production would have on groundwater?
Jessica Kolterman: There were concerns about the volume of chicken litter that the new poultry would create. People who are not associated with farms may not realize how much fertilizer is currently being used on farms or understand the regulations that govern that use. In reality, quite a bit of cattle manure and hog manure is already being used as fertilizer across Nebraska. Chicken litter shouldn’t be looked at any differently. We worked hard to set a high standard in order to mitigate these concerns.
Irrigation Leader: Were there any legal regulations that regulated how you disposed of that litter?
Jessica Kolterman: Actually, there were no regulations that applied to chicken litter, because it’s a dry substance. In fact, we went to the State of Nebraska and asked to be regulated. The state developed a permit that would hold our poultry growers to the same standard that other livestock operators are held to. In order to grow for us, poultry growers are required to get a state operating permit from
the Nebraska Department of Environment and Energy. That requires them to have a nutrient management plan, to develop nutrient budgets, and to track everything. They can’t just dump their litter on a field somewhere; it all has to be monitored and accounted for in a prescribed manner.
Irrigation Leader: What has been your experience with public relations during this?
Jessica Kolterman: As with anything that’s new, there were a lot of questions about how the project would work and how it would affect people. Our team committed to answering those questions and telling the story of the project through a strong public relations effort. At the beginning, we spent
a lot of time in front of church groups, civic organizations, chambers of commerce, and anyone else who wanted to learn more. We would go to their gatherings and events and discuss the specifics of the project. On one side, we talked about how the project would affect the local community and the region economically and in terms of job creation. We talked about the technology we’re hoping to use in the facility. We talked about traffic associated with the facility. We talked about our goal to be good environmental stewards with the processing facility and the surrounding buildings. We also discussed our relationship with the farmers and how we want them to be good stewards of the land as well.
We did everything from door-to-door canvassing, in which we answered people’s questions at their doors, to presentations at public forums and before formal bodies like city councils, local zoning groups, and natural resources districts. We spent a lot of time and energy trying to answer any questions that existed and to provide a picture of how the project would affect people in their day-to-day lives.
We have also built a safe, clean viewing corridor in our facility from which visitors can see our chickens being processed. There are no secrets or mystery about it. We’ve also worked with Costco to create a viewing room on one of our farms. If someone wants to see how the chickens are being raised, we can take people there and show them that we raise our chickens humanely and we treat them well.
Irrigation Leader: Now that your facilities are up and running, what have the results on the ground been? Have you had to make any adjustments?
Jessica Kolterman: One small adjustment, a good one, was that because the corn and soybeans here in Nebraska are of such high quality, our birds are growing a little faster than we initially expected. We were pleasantly surprised to find that the feed conversion was better than expected.
Generally speaking, most of the people who have visited our facility have had a positive experience. We had an open house with about 5,000 visitors and guests, and the feedback was positive. We have had a great deal of interest from people in coming to work for us. People who have heard about our company and want to be a part of our team come in every day. We have a staff of 660 people at this point and have done only limited advertising and marketing. There has been a lot of interest in our company and publicity about it. This is a respectful company with a good working environment; it takes care of its employees, protects the environment, and works to have a sustainable operation. We work hard to meet those goals every day.
Irrigation Leader: What is your advice for people considering building a similar project?
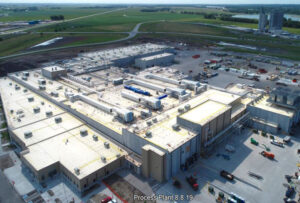
Jessica Kolterman: On the groundwater side, first of all, look at what the current regulations are. Make sure those regulations meet the standard that you want your company to meet. In our case, we added an additional layer of accountability for growers.
Second, you have to tell the story of what’s happening with your farmers or your facility. If you don’t tell that story, someone will fill that gap for you. In the absence of facts, people will often go looking for answers, and sometimes they find answers that aren’t accurate or up to date. From a public relations standpoint, we work hard every day to be accessible, to answer the questions that people have, and to paint an accurate and honest picture of what we’re doing. Keep getting as much information out there as fast as you possibly can.
Irrigation Leader: Was there anything else you wanted to touch on?
Jessica Kolterman: When we moved in, Fremont’s wastewater treatment system needed to be updated, and we were able to help provide some funding on the front end for those upgrades. Communities can look at the growth of large companies or large operations like this as an opportunity to update or upgrade their infrastructure without putting additional cost burdens on the average citizen. When Fremont upgraded its system, it was able to incorporate our needs while also addressing what it was lacking and what it needed to improve.
Jessica Kolterman works in external affairs for Lincoln Premium Poultry. She can be contacted at jkolterman@lincolnpremiumpoultry.com.