Trojan Technologies is a leading manufacturer of municipal, residential, and industrial ultraviolet (UV) light water treatment technologies. It has broad experience and a huge install base that includes under-sink systems purifying a few liters of water a minute, major municipal facilities that treat millions of gallons of water a day, and even off-grid installations that ensure safe water supplies in remote locations. In this interview, Trojan Technologies President Stephen Bell tells Irrigation Leader about the advantages of UV treatment’s flexibility and about Trojan’s work around the globe.
Irrigation Leader: Please tell us about the history of Trojan Technologies and about its current product lines.
Stephen Bell: Trojan was founded about 43 years ago as a toolbox manufacturer. Its starting point was that it had a new technology related to the UV treatment of water for contaminants. Over time, it made a number of acquisitions and grew significantly. I received a letter from the founder about a month ago saying, “I remember when we were valued at $285,000 and all the staff would come together on Monday mornings around a coffee table to look at the week ahead.” Things have grown by more than a thousand times since then. Trojan has added other businesses that work on industrial water treatment and residential UV water treatment. Our UV technology is not just for municipalities; it includes systems that you may have in your home, especially if you’re drawing water from untreated sources such as a well, borehole, or rainwater collection system. In addition to those, we are treating water in microelectronics and vaccination production facilities. We’ve broadened over the years to filtration technologies as well as pure water and softness technologies.
Irrigation Leader: How does UV light work as a water treatment method, and how does it differ from other treatment methods?
Stephen Bell: The technology works by sending light through the water that stops the reproductive elements of viruses and other contaminants. It’s all about stopping evolution. That’s what makes UV so flexible: It won’t change the fundamental makeup of water, but it will stop any further contamination or the growth of contaminants. When UV is used for contaminant removal, it is usually used with an accelerant or some other chemical. UV can be used in a multitude of different applications in many different ways, hence its viability as a treatment method for water types from drinking water to wastewater.
UV’s flexibility is absolutely a key advantage. When you switch on the system, it’s ready to go quickly. A chlorine treatment facility, by contrast, can’t be turned on and off instantly. Likewise, as long as you’re connected to electricity, you have the ability to generate UV and to disinfect water. You don’t have to worry about transporting truckloads of chemicals. The UV treatment process has also evolved to become energy efficient. Massive strides have been made over the past 40 years in terms of the energy needed to generate a certain dose or amount of UV. In the last few years, I’ve seen some customers who will install a new plant or upgrade their facility and receive a payback in 3 years or less based on electricity savings alone.
Irrigation Leader: How long does water need to be exposed to UV light for the treatment to be effective?
Stephen Bell: Generally speaking, the reactions in simple processes such as disinfection are incredibly fast, on the order of seconds. The question is more about how much UV energy is required to achieve the treatment goal. This relies on a variety of things, such as UV transmittance, which refers to how easy it is for the UV light to get through the water. Distance and intensity are also important. UV is not something like an activated carbon bed or tank that can require a certain amount of settling or contact time. We have small systems that treat 10–20 liters per minute and extremely large municipal systems that involve entire trains or even a 48‑inch diameter pipe that water is traveling through. The sizing and the speed with which water can travel through the system depends on the dose of UV that is required. The calculation is much more critical for large installations than for small ones, because there’s usually a safety factor. The pipes themselves are limiting factors in home installations or industrial installations.
Irrigation Leader: What can you tell us about the installation costs, energy consumption, and maintenance requirements of UV systems?
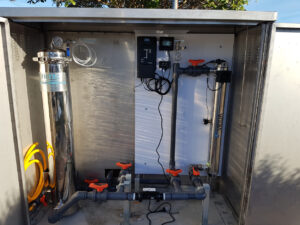
Stephen Bell: Obviously, those costs vary depending on the size of the system. When you have channels, pipes, or plants that are custom built for treating millions of gallons per day, UV forms part of a custom-built treatment train. In the case of smaller systems, people generally don’t build their houses around the UV system. The UV system or filtration system will be plumbed into a home via a normal ½-inch or ¾-inch pipe and generally won’t require much more energy than a simple household light bulb.
Energy consumption depends on the method of generating UV light. Medium-pressure lamps, which first emerged a few decades ago, require a large amount of energy as an input and are inefficient but allow you to have a small footprint for a large UV output. What we’ve been working on for the last few decades are low-pressure, high-output lamps, which are much more energy efficient than what we’d seen in the past. Today, customers are getting three times the UV from their lamps at much lower levels of energy consumption by moving to newer technologies. That also affects maintenance requirements. If you have fewer lamps, you require less maintenance. The new lamps are also more reliable, with guaranteed lifespans of up to 15,000 hours, sometimes more. Fewer lamps, longer lifespans, and higher efficiency mean less maintenance, lower costs, and more energy savings. Comparing a system from today with a system from 20–30 years ago is night and day. That’s what makes it attractive for some customers to upgrade their plants now.
Irrigation Leader: How does Trojan’s systems and its technology differ from those of other manufacturers of UV technology?
Stephen Bell: What we’ve focused on over the years has been maintenance and energy consumption. First, we work closely with customers to get the sizing right, especially on the larger plants. Second, to make sure that our systems are the most reliable, lowest-maintenance systems out there, we use a lower number of low-pressure, high-power lamps. If you look at some of our newer municipal products, our TrojanUVFlex and TrojanUVSigna systems require far fewer lamps and have a higher UV output than competitors’ products. That makes these products extremely attractive to customers. We also provide automated cleaning systems, which have chemical and mechanical cleaning elements that minimize maintenance requirements for operators.
Irrigation Leader: Where are your products produced, and how many countries are you active in?
Stephen Bell: We are active in close to 100 countries at this point in time. We have over 10,000 municipal installations and are approaching a million residential units installed. All our systems produced today in the cities of Guelph and London, Ontario. Our two Ontario production facilities produce our residential, industrial, and municipal units. There is a single engineering team that shares expertise between these product lines. That’s something that we leverage to bring the best from the municipal side of things into industrial and residential and vice versa.
Irrigation Leader: Are your products are available in or installed in New Zealand?
Stephen Bell: We do have installations in New Zealand. The majority of the demand in New Zealand for our products has been from municipal customers; however, our residential products have a long history and strong brand position within the private well/borehole and rain catchment markets and have been actively used in New Zealand for well over 10 years. One good example is the Taupō Water Treatment Plant, which uses our Pall water filtration system. Doing remote installations or installations off the municipal grid is also something we’re incredibly familiar with. In North America, we have thousands of customers, especially on the residential side, who are not living on a grid and who are using UV to ensure that the water they’re receiving, using, and consuming is safe for exactly that reason. Putting a system in without thinking about water content, sizing, maintenance, or cleaning can be quite risky. Consulting with a company like us that has broad, proven experience can be incredibly valuable. You want the system to work not only on day 1, but throughout the product life.
Stephen Bell is the president of Trojan Technologies. For more on Trojan Technologies, visit www.trojantechnologies.com.